
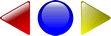
Diesel Lambda Sensors
Emissions control for the last thirty or so years for Petrol (Gasoline) powered engines has concentrated on the cleaning up of the exhaust emissions primarily through use of a catalytic converter. Conversely, emissions controls for diesels has concentrated on cleaning up the combustion itself, thus having a cleaner exhaust gas leaving the combustion chamber.
But during the last fifteen years, much time has been spent on developing catalytic exhaust emissions control for diesels, especially in the case of particulate emissions (soot), which is the primary cause for concern in diesel exhaust.
So why are diesels so sooty?
The Diesel combustion process in detail
Firstly it is useful to know a little about how the diesel combustion process occurs. Most of us know the air inducted into the diesel engine's cylinder is first compressed to a very high pressure, hence the name "compression ignition engine" (abbreviated to C.I.)
Once the air is compressed, we can then inject a fine stream of diesel fuel into it using an injector. Almost immediately, the fuel will spontaneously ignite because of the very high temperature. An average diesel engine compression ratio is perhaps about 15:1; the result of this is, by the end of the compression stroke, the temperature inside the combustion chamber will be about 650 degrees C, and the pressure about 500 psi. This is well above the so-called 'auto-ignition' temperature of diesel fuel, which is around 450 degrees C, depending on the quality of the fuel.
After the combustion of the diesel, the pressure inside the cylinder will rise further, to a massive 1000 psi, thus providing the downward force on the piston as it begins to descend the cylinder. Power is regulated by varying only the amount of diesel fuel injected - the airflow in a traditional diesel is largely unrestricted. We alter the amount of fuel injected by varying the on-time (duty) of the injector. Conversely, in a petrol engine (Spark ignition - S.I.) we have to vary both the fuel and the air.
Indirect Injection
Up until the mid Nineties, indirect injection (IDI) was used on small diesel engines as fitted to passenger cars. They never have used Lambda control and rarely had emissions controls of any kind, but are included here for comparison and reference.
The combustion chamber had a fundamentally different design to the later direct injection (D.I.) diesel which subsequently became dominant in passenger cars. Note that larger diesels and commercial vehicle diesels have always been the D.I. type. With reference to the diagram, it can be seen that the I.D.I. piston crown has a dished surface. Once the inlet valve has closed (as illustrated in Figure 19) and the piston is approaching the position shown, the inlet air is forced into an auxiliary circular chamber away from the main chamber. As it is pushed through the narrow throat leading to the chamber it gathers much speed, and due to the chamber's circular nature it swirls round and round very quickly. Then the diesel is injected, leading to good atomisation and charge distribution due to the swirling very hot (due to compression), high pressure mass of air.
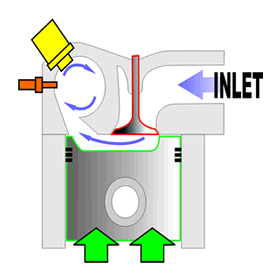
Figure 19 - Indirect Injection Combustion Chamber - Airflow - Blue, Piston - Green, Inlet Valve - Red, Injector - Yellow, Glow Plug - Orange
I.D.I has certain advantages. Because of the excellent atomisation the ignition delay is very short, and the engine will run more smoothly and a lower quality fuel can be used when compared with D.I. engines.
Because the remote chamber suffers a degree of thermal lag, a glow plug must be fitted to aid cold starting. This allows the chamber to be heated prior to starting so the heavier fractions of the diesel fuel can be ignited easily. Diesel fuel is a mixture of different oils or 'fractions' and the lighter fractions are included in the mix because they will ignite more easily in a cold engine. The heavier fractions have a slightly higher auto-ignition temperature and will only burn once the chamber is hot enough to vapourise them. A better quality diesel fuel will have a larger proportion of lighter fractions.
Direct Injection
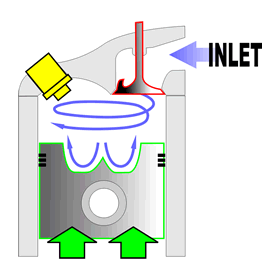
Figure 20 - Direct Injection Combustion Chamber - Airflow - Blue, Piston - Green, Inlet Valve - Red, Injector - Yellow
The Direct Injection fuel injector squirts fuel directly into the combustion chamber. The cylinder head is machined very flat and the piston has a substantially different shape. In order to create the swirling hot air like we had in the indirect injection chamber, the inlet valve is 'masked' which can be seen in Figure 20 (the raised part on the top of the red inlet valve). Along with a finely tuned angle to the inlet passage, the air is deflected into a circular path around the circumference of the cylinder. In addition, the curved recesses in the piston crown will create vertical swirl which will increase speed as the piston travels up the cylinder.
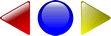