
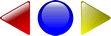
Cleaning up Diesel exhaust
Traditional diesels use mechanical injection systems. These evolved into so-called 'fly-by-wire' systems where the metering carried out by the mechanical pump was controlled electronically by an ECU, using solenoids and servo motors rather than a throttle cable and linkage to control the injection duty.
Passenger vehicle diesels were formerly 'indirect injection'; this involved
a separate chamber that carried out the first stages of combustion, with
the latter stages spreading out to the main chamber. This allowed fuel of
lower quality to be used, and gave a smoother power output, chiefly because
of the high air-swirl speeds attainable in the smaller, remote chamber.
Direct injection (D.I.) was the norm for passenger vehicles from the early
90's onwards; D.I. has always been used in heavier diesel engines but was
only acceptable in passenger vehicles once accurate electronic controls
had been introduced. None of these systems used lambda control.
High-pressure common rail Diesel injection
The first automotive common rail fuel system was developed by Denso of Japan, and used for commercial vehicle applications. The most popular system in passenger vehicles, developed by a group of companies including Fiat, then sold outright to Bosch, is termed variously (CDi, HDi, TDCi, DCi, for example). High-pressure common-rail injection represents the current state of passenger car diesel systems. All of the combustion phases detailed previously for the low-pressure injection systems apply, but different methods are now employed to overcome some of the problems.
As the name suggests, firstly, the injection pressure is raised substantially, from roughly 300psi in a traditional diesel, to about 2,000 psi at idle and up to 15,000psi at full load. This allows finer atomisation to occur when the fuel enters the combustion chamber due to greater velocity from the injector. Also, rather than the injector being activated by a mechanical pump and one-way valve, the injector is triggered electronically, just like in a petrol injection system. This allows very fine control of spray timing, and allows the ECU to combat some of the disadvantages of the C.I. process.
Diesel exhaust soot is caused by incomplete combustion due to localised lack of oxygen, but with fine electronic control of the injector the ECU can inject the fuel into the cylinder in stages, rather than all at once. This allows a small amount of fuel to initially pre-heat the chamber and finish burning before the main injection charge.
This main charge will then encounter favourable conditions - a higher initial temperature will mean the delay period (Phase 1) will be shorter, leading to smoother power delivery. This degree of control is only practical during part-load operation; during periods of hard acceleration the requirements for a rich mixture are still present, and it is during this phase that most of the soot is produced due to localised poor combustion. However, particulate filters can trap most of this in the exhaust system, which can be oxidised out as required by the ECU, by burning it away at high temperature.
Diesel Lambda sensors
This super-fine control of mixture strength allows Lambda control to be possible for these common-rail systems, and from about 2005 onwards this has become the norm. Motivating all these innovations are EU emissions regulations, which are becoming ever more stringent for Diesel cars after an initial phase of being allowed to lag behind the equivalent petrol-engine regulations.
Diesels are by nature lean burn engines, so require a wideband lambda sensor that can detect A/F ratios over a very large range. Silicone compounds are added to diesel fuel to ease transportation and for their anti-foaming properties, which poisons the lambda sensor over time, but additional measures are taken in the design of diesel lambda sensors in order to combat or lessen this problem.
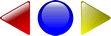