
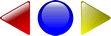
Types of sensor
There are three main types of lambda sensor -
- Zirconia - the most common and oldest type
- Titanium - Used on some BMW, Volvo and Vauxhall models with Siemens ECU, during the nineties (often called 'Titania')
- Planar - wideband sensor, found on the latest generations of engines from the 2000's onwards
The Zirconia type is also referred to as a 'narrowband sensor' and was the first type of sensor to be introduced. Titanium sensors offer many advantages over the Zirconia type, and are most commonly encountered on vehicles using the Siemens engine management system. The current generation of sensor is the 'Wideband' sensor, easily identified by it's multi-wire (more than 4 wires) harness. These are normally found on lean-burn engines, and some Japanese vehicles. Both Bosch and NGK produce wideband sensors, which have been used in non-automotive applications too.
Each sensor is tailored to each specific application. As well as the connector types and harness lengths, internal differences exist between sensors such as heater ratings, grounding arrangements, and most importantly the protection tube surrounding the sensing element differs in design according to the sensor's location in the exhaust system. Also an internal baffle may be present depending on all these other factors.
Zirconia Sensors
At the heart of the Zirconia sensor is a ceramic electrode made of ZrO2 (Zirconium Dioxide) coated with micro-porous platinum. This arrangement acts like a tiny battery, and it is this (very small) voltage that is measured by the engine ECU using a high-impedance input.
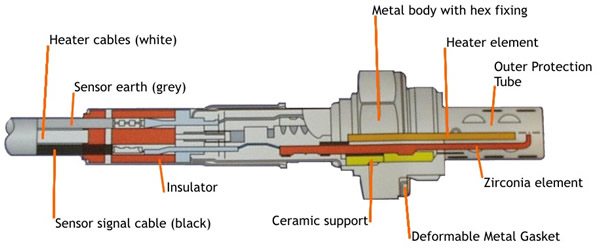
Figure 9 - Cutaway view of a Zirconia Lambda Sensor
The sensor element has two 'sides' to it - the outer layer and the inner layer - which are isolated from each other and exposed to different gases. The outer layer of the sensor is exposed to the exhaust gas stream immediately after or in the engine exhaust manifold, before the catalytic convertor. The inner layer of the sensor is vented to the atmosphere outside.
The sensor outer body and wiring harness should ideally be kept clean and free from oil and other dirt, which may block the vent. Some vents are located on the sensor body; other types vent at the far end of the harness. The sensor element is exposed to the exhaust gases inside the exhaust pipe, encased in a protective covering with holes to let the gases in and vent them out again. This protection can is an important part of the design which is often tailored to specific vehicle requirements.
Failure of the sensor due to element contamination (see our diagnosis page for failure modes of the Lambda) can happen on either surface of the element - exhaust-side or vent-side. This can be caused by either contaminants in the exhaust gas or in the engine bay.
The sensor element, made from Zirconium Dioxide, is right next to a heating element because the sensor only starts to work properly when it reaches 350+ degrees C. Although the exhaust gases are capable of heating the sensor up this much when the car is at speed, during cold start, idle and other operating conditions where the exhaust gases are cooler the assistance of the heater is needed.
OBD II cars have a downstream sensor, after the catalytic converter. Regardless of the type of the upstream sensor, the downstream sensor is normally a standard Zirconia type. Multiple sensors are also increasingly common, with manufacturers installing a sensor on adjacent pairs of cylinders on four cylinder engines, and on each bank in V6 engines. This is for more precise engine fuelling control, which in turn is legislated by emissions laws.
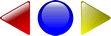